市場ニーズが多様化し、製造業は、量産型から多品種少量生産型への方針転換を迫られています。ERPなどパッケージ型の生産業務管理システムの導入に注目も集まりますが、一方で実は多くの企業が、組織内に潜在的な
そこで本コーナーでは、製造業を得意とする経営コンサルタントの中山幹男氏が、企業の抱える潜在的な問題の見つけ方や、その解決策を伝授。力強い体質へと変革を図るうえでのヒントをお伝えします。
成長の足かせは、部門間の連携不足
仕事がら、さまざまな企業のBOM表を目にします。BOM表とは、ご存知の通り、製造に必要な部材の構成、部材の品目や数、納期等を登録する表のこと。部品マスタとも呼ばれ、これを元に部品が集められ製品がつくられるという、製造前段の肝となるデータです。
こんな大事なものにも関わらず、整然とまとめられたBOM表を見ることは、滅多にありません。手書きで修正に修正を加え、判読が困難なものさえある。誰もが名前を知る大手企業からも、そんなBOM表が出てきます。
残念ながら、これが日本の製造業の実態です。その場しのぎの積み重ねで、それを全体に共有する連携ができていない。
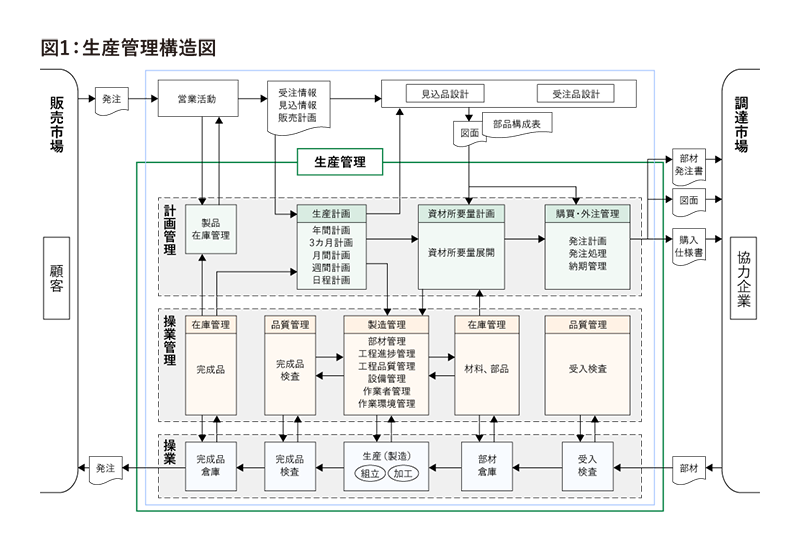
<図1>は、一般的な生産管理構造をまとめたものです。ひと口に生産管理といっても、幅広い業務内容が含まれることが見て取れるでしょう。この図は見込み生産の流れを示していますが、受注生産でもその点は同様です。
これらのプロセスをトータルに把握する部門が、日本の企業にはほとんどありません。コンサルティングに出向き、生産管理の全体図を見せてほしいと言っても、すぐに示してくれる企業は滅多にない。全体の指揮者が不在のまま、各部門が「どうしたら自分たちの仕事がまわしやすくなるか」と、個別最適を優先させている現状です。
実は部門間の連携不足は、企業の利益を大きく損ねます。私がこれまでみた企業の多くが、連携不足によって利益の10~20%をロスしています。さらに問題なのは、多くの企業がそのロスに気付かないか、気付いても「仕方ないもの」と受け入れてしまっていることです。しかしながら、ロスは、必ずなくすことができます。
とはいえ、なくすには全体を俯瞰する必要があります。一気通貫でみることで、一部門ずつみている限り気づかない、部門と部門の隙間に
具体的に、生産管理のプロセスの中の、ムダを生み出す課題についてみていきましょう。
単純なミスと、それを発見できない体制が問題
営業―生産管理間
営業部門で顧客から確定注文をもらい、生産管理部門はその情報をもとに生産計画を立てます。ここで起こりやすい問題は、以下の通り。
- 営業が過大な販売計画を出し、在庫が余ってしまう
- 生産管理が独自判断で営業の示す数字より少なく計画を立て、欠品が生じたり、飛び込みの注文に対応できなくなったりする
部品マスタに関わる部門
部品マスタには、設計部門と生産技術部門が関わります。設計部門が図面を引き、例えばA、B、Cという部品が必要だと登録する。生産技術部門はそれを元に「B、Cは外注で組み合わせてⅮという部品にして納入してもらう」などと判断して生産設計し、それぞれの個数と納期を登録。
その部品マスタを、生産管理部門が資材所要量計画の立案に使います。このプロセスで起こりやすいミスが以下の点。
- 設計部門、生産技術部門、それぞれの単純な入力ミス、計算ミス
- 設計部門から生産技術部門への情報の不足、不備
- 生産技術部門の生産設計ミス
部門間の連携がとられていれば、ミスは速やかに発見、修正されますが、互いに間違いを指摘せず、その場しのぎの対応をして部門内で解決してしまうと、部品マスタの不備がいつまでも残ります。
資材所要量計画に関わる部門
生産管理部門は、部品マスタおよび、部材在庫管理部門から来る在庫情報を見ながら、いつまでにどの部品を何個用意しようという、資材所要量計画を立てます。通常はMRPという資材管理システムをまわして計算します。起こりやすいミスは以下の通り。
- 在庫情報や部品マスタの間違いによる計画ミス
- 実在庫数とデータ上の在庫数の照合不足による計画ミス
- MRPの入力データ間違いによるミス
購買オーダーに関わる部門
資材所要量計画に基づいて、購買部門が部材メーカーに発注します。
- 資材所要量計画の間違いによる誤発注
- 注文書の記載ミス、発行ミス
- 部材メーカーからの返答の確認不足や管理不足による納品もれ
部材在庫管理に関わる部門
- 実際の在庫数の確認不足
- 実在庫の情報の伝達ミス
- 入出歴処理のミス
これらの結果、製品の組立時に部材が入荷されずに生産ラインが手待ちになったり、また緊急で部材メーカーに対して、「割高になってもいいから、急いで◯個用意してくれ」などとオーダーすることになったりして、余分なコストがかかります。
ところが、「発注ミスが生じるのは当たり前」と考え、そのコストを削減しようとせず、さらには急ぎの発注書の書き直しに備えてパートを雇っているという企業すらあります。
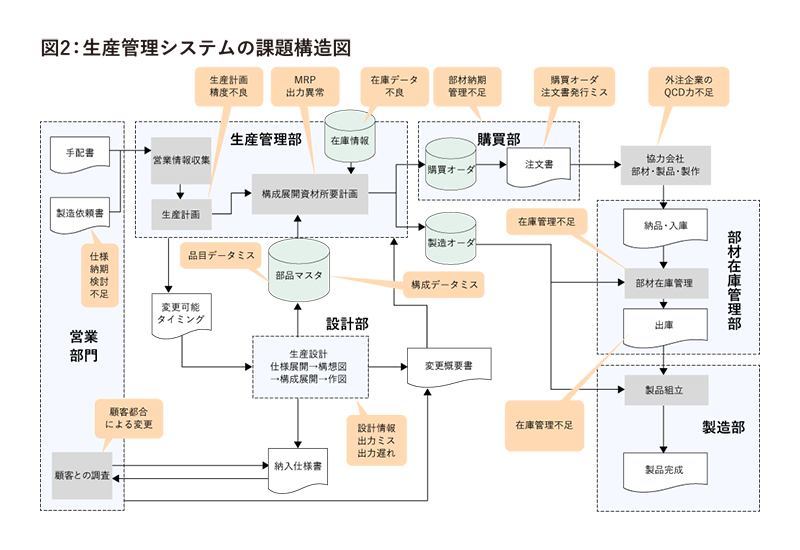
30年前の生産管理構造。このままでいいですか?
かつて自動車メーカーは、「最高性能の独創的なクルマ」をつくることを大命題として、開発設計部門が設計図を描いていました。しかし工場の生産技術部門がその図面を大幅に描き直していたのです。
ご推察の通り、開発設計部門の設計図は何よりも機能・性能が優先されたもの。量産のものづくりは念頭になく、そのまま図面では生産ラインにのせられないからです。
当時は自動車メーカーだけでなく、日本の製造業は設計開発部門が図面を描き、生産技術部門がこれを手直しし、生産現場の力でものづくりを可能にするバトンタッチ方式が一般的でした。このスタイルで1980年代以降、日本はものづくりにおいて世界ナンバー1といわれるようになりました。
それから20年、30年と経つ中で、自動車メーカーの開発プロセスは開発設計部門、生産技術部門、製造部門が開発の早い段階で協力して、設計図に機能・性能だけではなく、ものづくりの視点も組み入れるフロントローディング開発・コンカレント開発の仕組みに大きく進化しました。これにより開発のリードタイムの短縮、量産段階での設計変更の減少を実現。他の業界のメーカーも日本のものづくりの優位性を生かしつつ、開発段階で部門間の連携を生かす仕組みづくりを構築、実践しています。
こうして、量産以降の生産管理プロセスについてIT化は進みました。しかしその一方で、全体最適化を図る仕組みづくりは、未だに十分ではありません。その結果が、先述のような、互いに連携をとれば容易に発見でき防ぐことのできるロスの続出です。
なぜ、部門間連携がとられないのか。それは繰り返し述べているように、全体を俯瞰的に眺める役職が置かれていないからです。各部門の実情を把握し、全体最適を図ることができる人がいない。
また、かつては組織内で協力し、チームとしていいものをつくろうというムードがありましたが、ITが普及した今は、個人最適を求める風潮にあります。その影響もあるのかもしれません。
一時期、企業間で連携し、不要な在庫を減らそうというSCM(サプライ・チェーン・マネジメント)が流行しましたが、結局あまり定着していません。部門間の連携すらできていない企業に、企業間で連携ができないのは当たり前といえるのではないでしょうか。
そうした中で、多品種少量生産型への市場ニーズはますます高まっています。部門が部門の仕事のしやすさだけを追求して、勝っていける時代ではなくなったのです。
さて、どうしますか。
業務プロセスの俯瞰的な見直しが不可欠
近年、企業が相次いでERPなどパッケージされた生産業務管理システムを導入していますが、多くの企業で、十分に機能していません。
「システムが悪い」「うちには合わないようだ」と断じる経営者もいますが、システムの問題ではありません。問題の本質は、生産管理パッケージに適合するように生産管理業務を見直したり、改善したりしないことにあります。生産管理業務の体質改革をしない限り、高価なシステムを導入しても宝の持ち腐れになってしまうのです。
したがって、自社の体質を改善したいなら、まずは生産管理構造を明らかにし、上記の例を参照して、自社の業務プロセスのどこにどのような問題があるのか探っていくことが重要です<図2>。
そのうえで、問題を生み出す構造を改善していくことが強く勧められます。私たちコンサルも、生産管理システムの導入にあたっては、まず各部門にヒアリングし、業務プロセス全体のどこに不整合があるか洗い出し、修正を図ります。全体の見直しなくして、生産管理システム導入の効果はあり得ません。
今回は、プロセスごとに生じやすいロスと、それを生み出す不整合の例を紹介しました。次回は、どうやって改善していくか、具体的な処方箋をお話しします。
中山 幹男(なかやま みきお)
株式会社A&Mコンサルト 代表取締役
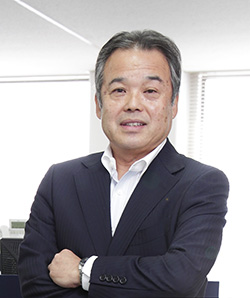
1978年、大阪大学工学部機械学科卒業後、大手自動車メーカーに就職。最先端の開発システムにふれながら、ものづくりの厳しさと喜びを知る。90年、大手コンサルティングファームの経営コンサルタントに転身。韓国の大手家電メーカーを手始めに製造業中心とした企業の事業再構築、開発改革、収益改善、生産性改善等多種のコンサルティングテーマを実践する。97年にA&Mコンサルト設立。代表取締役に就任。コンサルティング事業の推進の傍ら、ベンチャー・中小企業支援や、若手コンサル及び経営幹部の養成を推進。立命館大学では、産学協同アントレプレナー教育プログラムゲスト講師として登録。経営の考え方、自動車開発の現状などさまざまなテーマで講義を実施した